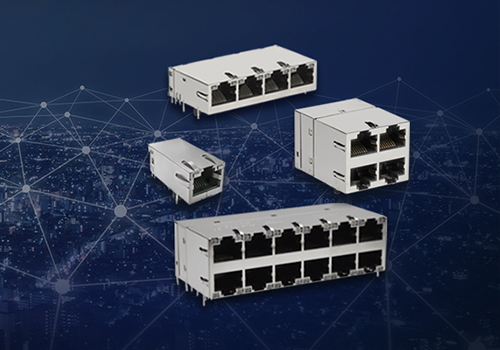
Ethernet Invades the Industrial Space
Ethernet is becoming the dominant communication protocol for industrial applications. Industrial ethernet connectors must meet IEEE 802.3 10/100/1000BASE-T electrical interface requirements while maintaining high reliability.
Download PDFThe growth in adoption of Ethernet as an industrial communications protocol has played a key role in this evolution of the smart factory. Initially restricted to the control and information levels of the factory, a number of extensions to the original IEEE 802.3 protocol have been ratified by the IEEE, enabling Ethernet to support the deterministic requirements of industrial processes. These extensions have since become open standards, widely deployed within industry, and enabling exponential growth in Ethernet deployment in industrial environments.
Design Considerations for Industrial Ethernet
Ethernet is rapidly becoming the predominant networking technology within the industrial environment, with a number of recent IEEE 802 Ethernet sub-standards covering the mechanisms required to support real-time communication. With the growing number of factory systems using Ethernet equipment, designers must ensure that networking modules can survive the harsh conditions of the factory environment. Factors such as ruggedness, operating temperature range, dust, electrical noise and vibration must be taken into account when choosing components. The ubiquitous RJ45 connector, for many years the main-stay of network cabling, is still the connector solution of choice in the factory environment and this article looks at some of the factors that must be taken into consideration when incorporating these connectors into factory systems.
Ethernet Changes in Industrial Environments
The continuing drive to improve productivity and return on assets has seen year-on-year growth in the levels of factory automation and a proliferation of connected devices. The deployment of robotic systems is increasing rapidly with their use moving from the traditional assembly line to smaller, more flexible applications, including collaborative workspaces, where human operator and robot work together. This increase in automation levels has been facilitated by the development of a number of common standards, fostering development of open-systems, ensuring interoperability of a larger range of devices from different manufacturers.
The growth in adoption of Ethernet as an industrial communications protocol has played a key role in this evolution of the smart factory. Initially restricted to the control and information levels of the factory, a number of extensions to the original IEEE 802.3 protocol have been ratified by the IEEE, enabling Ethernet to support the deterministic requirements of industrial processes. These extensions have since become open standards, widely deployed within industry, and enabling exponential growth in Ethernet deployment in industrial environments.
Solutions for Ethernet Connectivity - MagJack® ICMs
ICM SolutionsThe Ongoing Evolution of Ethernet
The Ethernet protocol spans Layer 1 (physical) and Layer 2 (data link) of the OSI layer-model and describes how networked devices can format data for transmission to other network devices on the same network segment, and how to put that data out on the network connection. Initially designed to run over coaxial cables, a typical Ethernet LAN now uses special grades of twisted pair cables, or fibre optical cabling. Ethernet standards are steadily evolving to embrace new media, higher transmission speeds and changes in frame content and functional requirements such as 802.3af, defining Power Over Ethernet [POE].
The most commonly installed Ethernet system within the industrial environment is 100 BASE-T ("BASE-T" signifying use of twisted-pair cabling) providing transmission speeds up to 100 megabits per second (Mbps). Gigabit Ethernet provides speeds of 1000 Mbps (1 gigabit or 1 billion bits per second) and 10 GbE, or 10-Gigabit Ethernet, provides up to 10 Gbps. Higher speeds are constantly under development for standardization.
PHY is an abbreviation for the physical layer of the OSI model and refers to the circuitry required to implement physical layer functions. The Ethernet PHY is a component that implements the Ethernet physical layer portion of the 1000BASE-T, 100BASE-TX, and 10BASE-T standards and the PHY functionality is usually implemented in a chip which interfaces between the analogue domain of Ethernet's line modulation and the digital domain of link-layer packet signalling. Figure 1 gives an overview of the functionality implemented by a PHY device.
Figure 1: Ethernet PHY Connection with MAC and Physical Medium
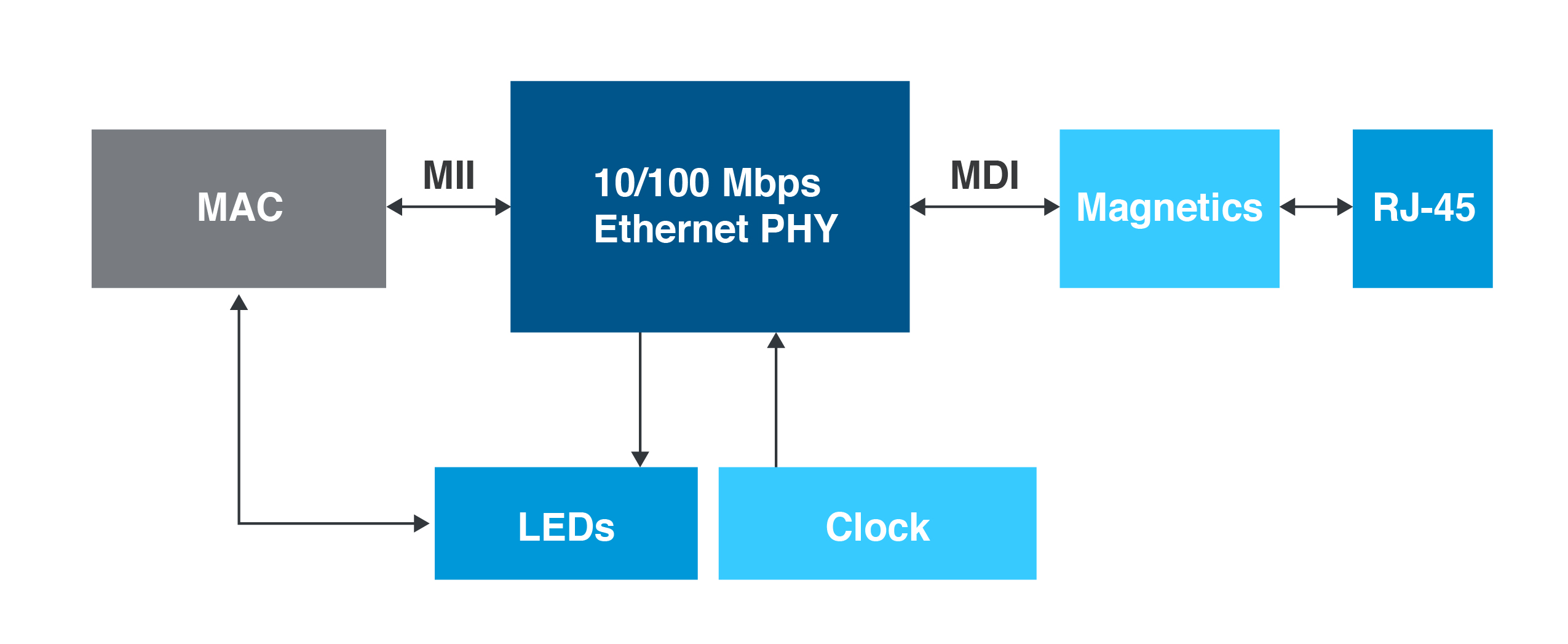
From Figure 1, it can be seen that there are two other important components making up the Ethernet PHY functionality. The “magnetics” is an analogue circuit designed to meet the electrical interfacing requirements of the IEEE 802.3 10/100/1000BASE-T specifications, allowing different nodes on the Ethernet network to connect over long distances. Magnetics address the key electrical interfacing requirements, including electrical isolation, signal balancing, common-mode rejection, impedance matching, and EMC improvement. The RJ45 connector, a low-cost eight-position 8P8C, has long been the mainstay of Ethernet connectivity, and is found on all Ethernet cables in current use. Any PHY board must therefore include a suitable RJ45 connector.
Supporting the Demand for ICMs in the Industrial Ethernet Market
Nowadays many connector manufacturers are delivering Integrated Connector Modules, (ICMs), in which the magnetics circuitry is built into the RJ45-type connector block. Using ICMs in the design of a PHY board offers a number of advantages, including lower component count - leading in turn to lower production/assembly costs, potentially better EMC shielding of the sensitive cable-side signals by the metal shield, and a smaller PCB footprint. ICMs also enable the PHY module design to be completely in the digital domain, with the analogue circuitry being packaged within the connector.
As the inventor and largest supplier of Integrated Connector Modules (ICM), Bel Magnetic Solutions, a Bel group Company, offers a wide range of Magnetics for communication, industrial and commercial applications. Bel’s extensive portfolio includes 3 ICM products which are specifically aimed at the industrial Ethernet market, where reliable, low cost connections are required in hostile environments, with operating temperatures between -40°C and +85°C. Suitable for a number of applications, including Industrial Ethernet controllers, Machine control boards, Ethernet lighting controls, Industrial Wireless access points and Industrial video display units, the ICMs are summarised in Table 1 below.
Table 1: BEL TRP ICMs for Industrial Ethernet Applications
Adapted from Bel data sheet - Industrial Ethernet MagJack® ICMs
Compatible with all major 10/100Base-T and 1GBase-T PHYs, these ICMs are small, easy to use and are designed to handle the stress and strain of factory life. The connectors are durable with a long operating life ensuring extremely low failure rates and operate between -40°C and 85°C. Options for IR reflow compatibility and tape-and-reel packaging support automatic insertion onto the PCBs, further reducing module production costs.
Figure 2: BEL MagJack® ICMs
Source: MagJack ICM Product Guide
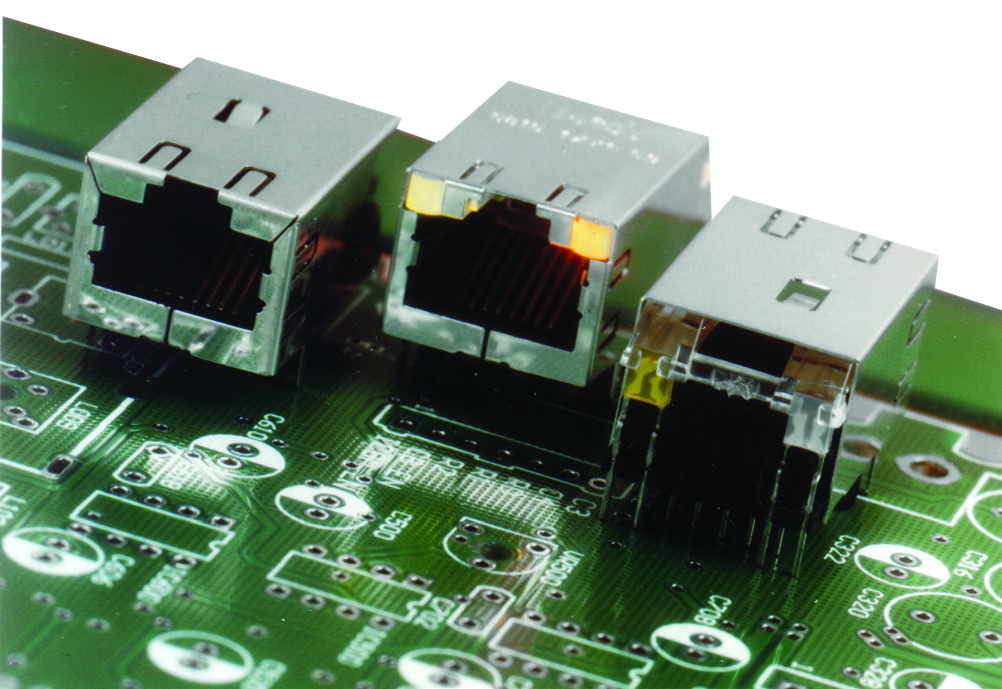
MagJack® ICM Ethernet Product Selection for MARVELL™
Approved Bel/TRP connectorsLeader in ICM Solutions
As Ethernet becomes the dominant communications protocol in the factory, more and more industrial machines, including a wide range of robotic systems must be connected to Ethernet networks. Designers of industrial-specification networking devices, such as Industrial Ethernet controllers and Machine control boards, must choose components carefully, with key considerations being ruggedness, lifecycle and cost. ICM modules have a key role to play in ensuring durable and reliable connectivity in hostile environment; these connectors must not only provide the necessary mechanical durability but their electrical performance is also critical in the hostile and noisy factory environment.
Explore Bel's Variety of Ethernet Solutions
Bel Magnetic Solutions offer an extensive line of Integrated Connector Modules (ICM), where the Ethernet magnetics solution is integrated into a connector package. The ICM product line covers every Ethernet application on the market today. Our products include one of the broadest ranges of magnetic based solutions for high-speed networking and computer applications. ICMs cover a range of Ethernet speeds and technologies from 10/100Base-T, 1GBase-T, 10GBase-T, and Power over Ethernet (PoE).